Design for Minimalism
We start our journey in Designing for Manufacturability first by minimizing parts! Hope you're excited, 🤓 because engineering products with the least amount of parts is one of the most fun and iconic engineering challenges!
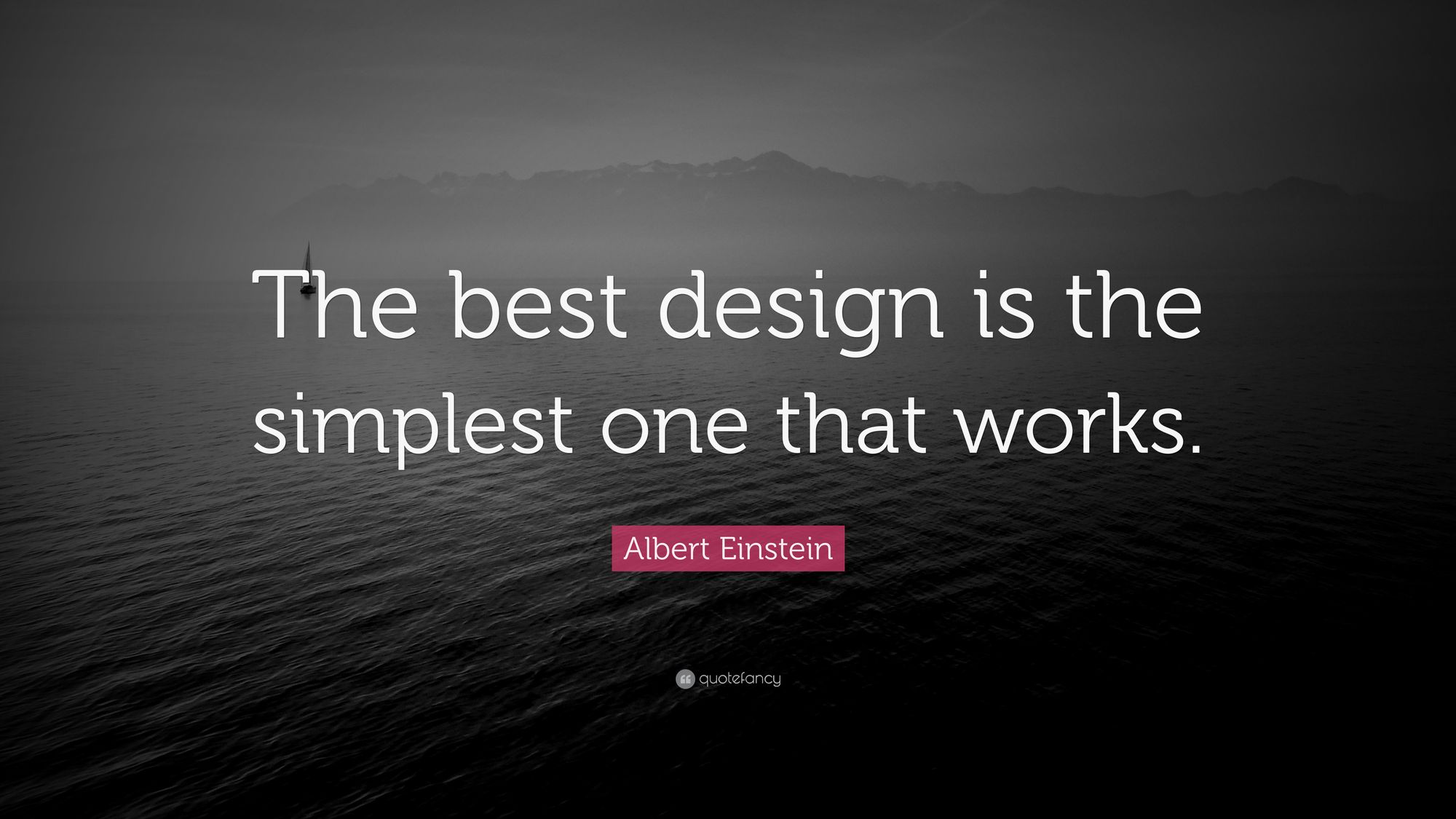
Why we start by minimizing parts?
When starting any new product design, we first focus our DFM efforts on minimizing parts. Why start here? Here are two very important reasons:
1. More parts means more work!
More parts result in more work for everyone! Parts lead to drawings, documentation, receiving, stocking, paperwork, potential assembly errors. If you can minimize this work from the start of a project, you'll save yourself a ton of work!
2. The longer you wait, the more difficult to minimize parts later.
This is especially true when formal testing and statistical qualification is required. Making dramatic design changes (like reducing parts) becomes very difficult once the design begins to lock down and become frozen.
In addition to the two reasons listed above, there are many other reasons why minimizing parts dramatically helps designs in the long run. These include:
- Less parts improves quality (less that can go wrong)
- Reduced cost (less to buy)
- Reduced lead time (less to procure)
- Reduced direct labor (less to assemble)
- Reduced purchasing and receiving activities
- Reduced warehouse storage and cost of inventory
- Often accelerates time to market (because of added efficiency from all listed above)
DFM frameworks to aid in minimizing parts
So, how do we minimize part count? First and foremost, this answer lies in engineering creativity! That said, there are some well developed tools that can also aid in this process and are listed as follows.
Theoretical Minimum Part Count
Boothroyd Dewhurst, Inc. were among the first to officially publish tools specifically for Design for Manufacturing (DFM) and Design for Assembly (DFA), and they made note of the importance in minimizing part count early in the process. The theoretical minimum part count (TMPC) was published by them as a simple tool for aiding in the reduction of parts.
How this works? One simply assesses each part interface as the device is assembled and asks these questions:
- Motion: Do the parts being assembled need to move relative to each other?
- Material: Do the parts being assembled need to have different material properties for proper functionality?
- Serviceability: Do the parts being assembled need to be separate for serviceability reasons?
If the answer to all these questions is no, one can potential to reduce parts by merging the two parts into one.
Do you need that extra part? Remember these questions: Is it separate for Motion? Material? Serviceability? If no, it can potentially be removed!
TRIZ - Function Model and Trimming
Dating back to the 1940's, TRIZ is a Russian acronym that stands for Theory of Inventive Problem Solving. TRIZ provides a wide array of problem solving tools, but one such tool, Functional Modeling and Trimming, has gained popularity in the DFM space.
How it works? The basic premise of functional analysis and trimming is a simple:
- List the needed functionality of the system
- Assess the components within the system and their purpose in the greater system functionality
- Ask for each component: Can it's function be performed by another component within the system? Thereby, eliminating (or trimming) a part
Trimming exercises are especially ideal on problematic components with quality issues. Â Trimming these components can significantly improve the overall quality of the product.
Other Notable Frameworks
Another way of looking at Design for Minimalism is the idea of form follows function, popularized in the late 19th & early 20th century in both Architectural and Industrial Design. Similarly, this principal emphasizes that designs should first meet its intended function.
Furthermore, even this rule builds upon another ancient Roman engineering philosophy authored by Marcus Vitruvius Pollio, (the actual Vitruvian Man) "firmitas, utilitas, venustas" — designs should be 1st solid, 2nd useful, and finally beautiful!
"firmitas, utilitas, venustas" [designs be solid, useful, and beautiful] - Marcus Vitruvius Pollio,
The DFM counter culture - Breaking the frameworks!
So, we minimize parts simply by completing the analysis above, right? ...🤨 wrong! Though these tools can be very helpful, they are simply frameworks and never a substitute for innovative thinking. Moreover, creative thinking really requires us to break the frameworks! Let's take a deeper dive into breaking these frameworks with critical thinking. 🤯
Be cautious of "Design Efficiency"
Shortly after the Theoretical Minimum Part Count (TMPC) tool was created, the management powers that be realized one could create an efficiency metric by dividing the TMPC by the actual part count. Doing so is often never a good idea and here are some reasons why:
- Higher efficiency doesn't always mean better to manufacture. Sometimes, the act of combining parts makes them so complicated that the parts can't be manufactured themselves!
- Answers to the TMPC questions can be subjective... and that's not a bad thing! Yes, people can complete the TMPC analysis for the same design and come up with completely different numbers. One might think to add more rules in efforts to "proceduralize" a final metric. This a bad idea and completely misses the point. The beauty of TMPC is that people can brainstorm and have different and diverse ideas for how to minimize parts! It's best done first individually by each member within a team, and then later used as a form of creative discussion within a team.
- The idea of Design Efficiency is not-actionable. As we have mentioned, Design Efficiency is derived subjectively. Â A higher score does not always meaning better. Furthermore, the derived number leads to no actionable analysis - e.g. Is 50% good or bad, and what should this metric lead us to do about the design? Your guess is as good as ours? Here are some better metrics to track: Total Part Count, Total Material Cost. Observe how these metrics compare to a baseline and brainstorm what can you do to improve. Â More on this in the articles to come.
Instead, cultivate curiosity!
As we mentioned above, the beauty of TMPC is the subjectivity and diverse answers! You want to encourage and cherish how people may have arrived at different answers and what their underlying thoughts were. Sometimes, people come to very creative ideas for how parts can be minimized where others could not.
- Here's an example: How many parts does it take to create a box with a hinged door? The door needs to move relative to the box, so you need at least 2 parts right? ...wrong! How many parts does a pillbox have? Plastic living hinges are a great example of thinking outside the frameworks. The below pillbox is just 1 part!
Don't miss the trade-offs!
As mentioned before, minimizing parts can sometimes work against you, driving so much complexity into the component that it causes other manufacturing problems. These trade-offs are best measured from a birds-eye perspective on the entire assembly. What does the proposed configuration ultimately do to the overall material costs, quality/yield, labor? These all can be measured in dollar value to see if you are indeed improving the manufacturability. More on this in the articles to follow.
Avoid "formally" completing these as paperwork activities
Design for Manufacturability & the word "formal" almost never go well together in our honest opinion. Often, one ends up spending too much time on a paperwork analysis, that could have been better spent actually designing better products!
You may have heard Tom Wujec's TED talk about building Marshmallow Towers and how kindergartners seem to always beat post grad students in this challenge (see below):
Our best advise - be the kindergartner!
What's better and more effective than doing formal analyses? Playing like a kindergartner! Let's not over complicate these tools, as they are truly intuitive in nature. You especially don't need to formalize early on. Â Instead focus on brainstorming, testing, and iterating. Maybe you can formally write out what you did with these frameworks later, once you're happy with your design so that you can communicate all the work you put in.
Final Thoughts
At the heart of Design for Minimalism is a timeless engineering challenge - how can I design with the least amount of parts? 🤔 #challengeAccepted? 🤓
There are some frameworks and tools that can help. These are best utilized intuitively and informally while brainstorming and iterating designs early on. They can later be documented as a good communication tool, if useful. While they can be very helpful, they are not a substitute for critical thought!
So, as always, trust and utilize your engineering intuition first, and be the kindergartner. Happy part minimizing!
Next Up:
This site is powered by
