Design for Standardization
Over 100 years ago, Henry Ford summed up standardization really well, simply as follows:
To standardize a method is to choose out of many methods the best one and use it.
Or, perhaps even more wisely put:
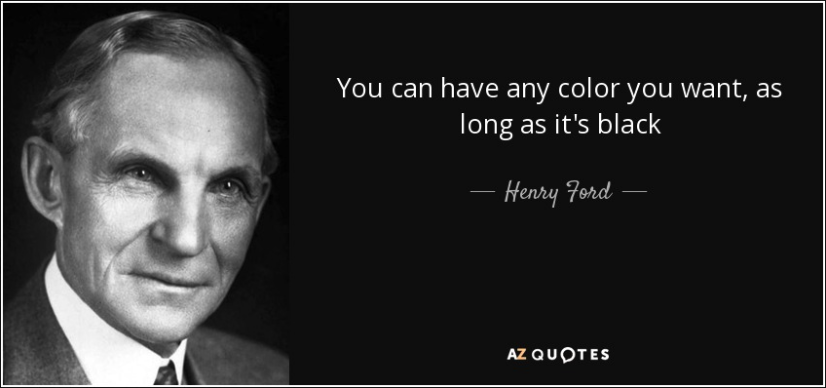
The idea of standardization is as simple as that! Seek out what works the best use it wherever possible.
The DFM Challenge: Design for Standardization!
Though the principals behind standardization are simple, the act of designing "the standard" can be quite challenging and rewarding. There's no limit to how far you can go with this. Questions to ask yourself when you design your next component: Could this part be used on multiple parts of the assembly or on other products? What features might you need to change in order to do that? Is the design great enough that all other products would want to use it?
But first, why standardize?
There are many benefits to standardization. Here are just a few:
- Reducing Costs: Aligning to standard components results in higher component volumes and less variation. Higher volumes means lower component costs. Less part variants means less inventory types to store and manage.
- Improving Quality: Aligning to standards means more learning and attention can be spent on fewer parts. That brings better attention to detail on on perfecting the design. It also brings familiarity across the organization so that vendors, purchasing, and operations can dedicate more focus on fewer things and develop deeper subject matter expertise.
- Improving Productivity: All of the above lead to better productivity! Part familiarity, less inventory to manage, more attention to perfecting quality, all of this leads to better operations overall.
Types of DFM Standardization
The idea of standardization spans far outside the realms of DFM, across manufacturing, operations, and beyond. That said, there are three aspects of standardization that are particularly relevant to DFM, which are as follows:
Design to Leverage
Design to leverage what exists and is best suited for the application. This is a fundamental concept for DFM. We should make our designs work with the best common components that we know of.
Design Multi-functional
We should next try to further the above idea, by creating our own standards! When you design a new part, you may ask if it can be used somewhere else. Sometimes, that requires changing or adding the features on that part, resulting in trade-offs that should be analyzed.
Designing multi-functional parts is truly a creative and rewarding challenge. There's no limit to haw far you can go with this. Can you make your part work on other areas of the assembly, or furthermore a common part across many different assemblies?
Design Modular
This concept builds upon the prior two, but focuses on standardizing sub-assemblies. The question that one should ask: Does it make sense to break apart a larger assembly into modular sub-assemblies with a common standard interface?
Benefits of doing so may include: First, breaking down an otherwise complicated assembly into simpler chucks, from which focused design teams can divide and conquer. Next, depending on how we break down the assembly into functional sub-assemblies, we can look for where those functional sub-modules can be used on other designs. Hence, we then focus on making really good functional sub-modules that can be use for many devices and applications.
Design for Standardization and DFM counter culture
It's important to note that DFM is about balancing tradeoffs with critical thought. There is no such thing as actually achieving DFM! It's instead a never ending goal that we should always aspire to. With that comes strategy and decision making, and there isn't really a right or wrong answer here. When it comes to Design for Standardization, please keep in mind the following standardization paradoxes.
Avoid over bureaucratizing standardization
As a company starts to embrace standardization, it's all too easy to slip into the idea of formalizing and proceduralizing use of standard components, assemblies, etc. Doing so can be a dangerous path and should be done with great caution.
Conversely, even Ford is quoted with emphasizing that one should think of "standardization as the best that you know today, but which is to be improved tomorrow."
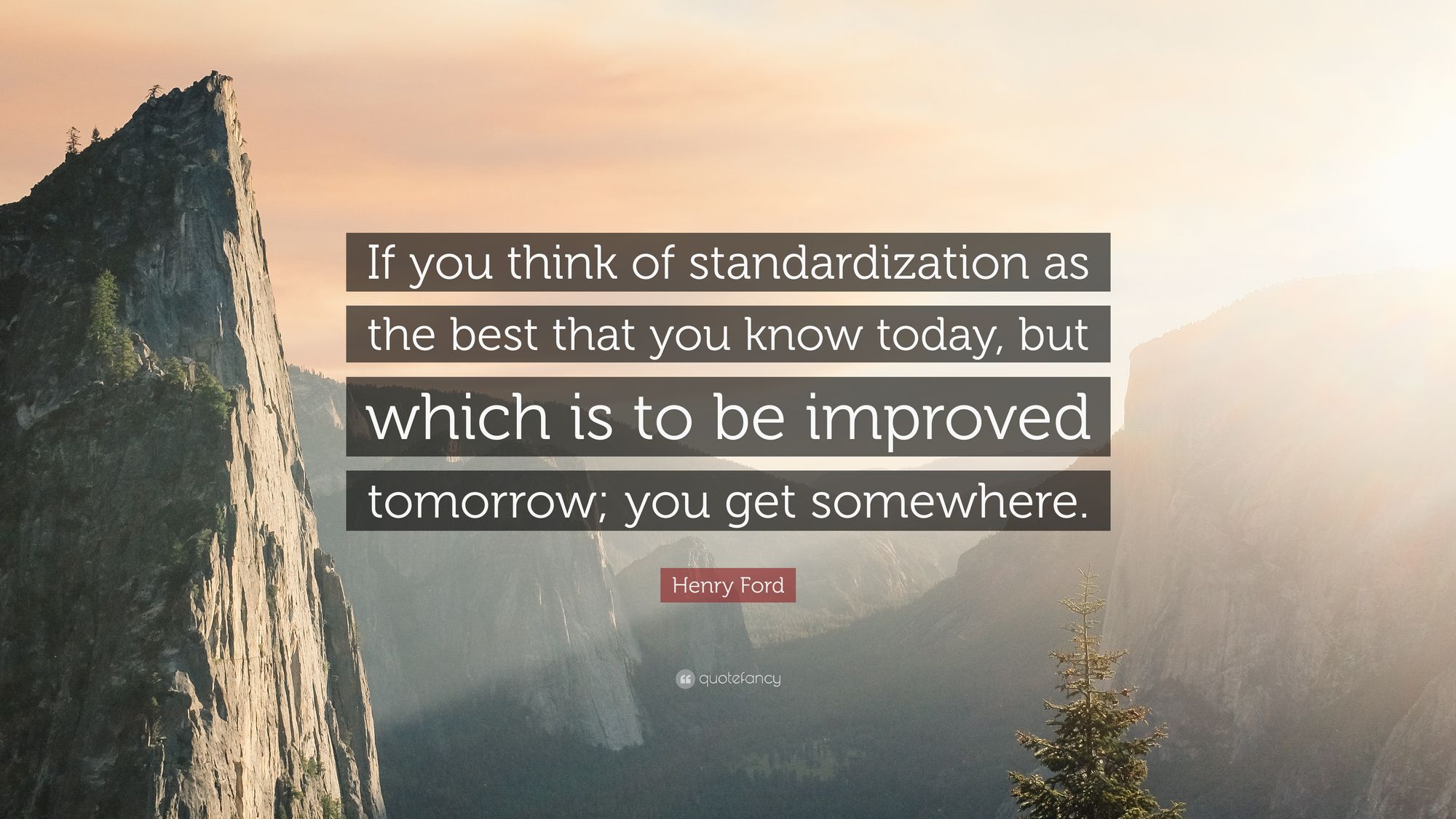
More importantly, he followed that quote with:
If you think of standards as confining, then progress stops
This underscores the dangers of going too far with standardization. Rules and bureaucracies, lead to creative frustration, which often makes talented people want to leave.
Standardizing across larger organizations can be challenging. We are often asked what's the best way to do this. Often companies jump to the idea of a standard parts catalog. This may be helpful, however its best to keep this light (e.g. try wiki crowd sourced recommendations instead of an enforced procedure)!
What we truly recommend: Don't underestimate the power of the water cooler!
Imagine if instead of making global standards, you spent the extra effort doubling down on creating a truly awesome water cooler type infrastructure. Meaning, engineering a culture where teams can cross pollinate and share ideas frequently and easily. That could be by means of campus facilities (a coffee bar etc.), encouraging events/mixers, encouraging knowledge sharing, or designing your campus to be a giant circular spaceship... 🍎. Engineering an awesome culture is truly a creative and rewarding task!
Please do re-invent the wheel!
When we talk about standardization, too often we hear the saying "Don't re-invent the wheel." Our response: if you have an idea for a better wheel, then please do re-invent! The danger in not doing so (over standardizing) is in destroying innovation.
For whatever you choose to make a standard, it can almost certainly be said that one day there will be something better. Innovative cultures must both embrace and facilitate this notion, or be left behind. We recommend rather than proceduralizing a standard, focus on ways to facilitate the process of constantly seeking and validating the best solutions and then finding ways to implement them across the organization as quickly and efficiently as possible.
Standardize only to a degree that makes sense
Standardization is not the end all be all. Remember, even Ford eventually released several vibrant color variations. Perhaps early on, there was a need to budget and limit colors to fulfill a vision that everyone can afford a car. However, as the company grew and the automotive industry developed, certainly if Ford continued to offer only black cars, it would quickly be left behind. Hence, we standardize to a degree that makes good business sense.
Final wrap up
Our Design for Standardization challenge is in how elegantly we can design components and sub-assemblies to be used across multiple applications! Those modules should reduce cost, improve quality, improve productivity. We should aim to design in a way that leverages the best that we know. We should also aim to design multi-functional parts and sub-assemblies that create new standards! Finally, the organization should take care in not going too far with standardization. It's important to always seek and encourage better solutions and to do what makes good business sense.
Next Up:
This site is powered by
